BLOG
2019.04.19 update
Importance of maintaining Excavators
Mini excavators have evolved dramatically in the past 15 years. Enhanced systems and capabilities have allowed them to become workhorses on jobsites, spending long days trenching, grading, clearing and loading.
The best way for owners and operators to protect assets and keep them working at optimum levels is diligence in following your manufacturer’s routine maintenance schedule.
Here are some tips for compact excavator maintenance for your uptime and safety.
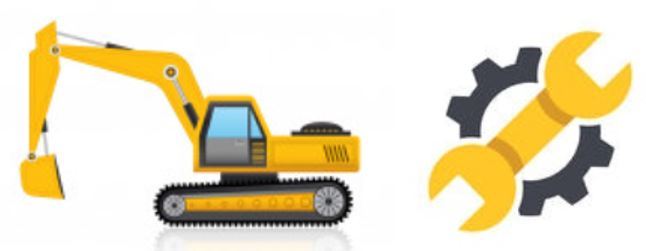
1. Fluids and lubricants
An effective maintenance regimen starts with a daily check of fluids, including coolant, hydraulic fluid and engine oil. If any of these levels are low, be sure to refill with the manufacturer’s recommended type of fluid, paying particular attentions to classifications, as well as viscosities for the operating environment. It’s also important to keep these areas dirt free and use clean rags while checking levels to avoid contaminants.
A machine system that’s experienced some of the most significant change is engines. Today’s compact excavators are equipped with various levels of emissions-compliant engines that may have unique lubrication requirements. Manufacturers are matching oils to their advanced engines to ensure the proper operation of exhaust after-treatment systems.
In addition to engines, it’s also important to regularly lubricate the machine at recommended intervals, taking into consideration the application and temperatures the machine will be working in. Manufacturers typically recommend the use of a quality lithium-based multipurpose grease to lubricate all key pivot points, including cylinders, booms, blades, buckets, arms and slew bearing components.
2. Filters
There are multiple filters on a compact excavator for the fuel, engine, air and hydraulic systems, and each may have different service intervals. When the filter is dirty or completely clogged, it can directly impact performance and compromise sensitive components. The majority of industrial excavators have air filter restriction indicators designed for the purpose of alerting operators to maintenance needs. To avoid system contamination, it’s critical not to remove the filter until the required time.
3. Fuel
Most manufacturers specify the use of clean, high-quality No. 2 or No. 1 grade diesel fuel. Operators with machines that routinely operate in colder climates may prefer the option of specially formulated blends designed to prevent gelling. At a minimum, ultra-low sulfur diesel fuel must be used in these machines to reduce exhaust emission levels. Depending on jobsite conditions, owners and operators need also to be aware of water separation that can occur in a fuel filter as a result of a lower quality fuel supply.
4. Undercarriage
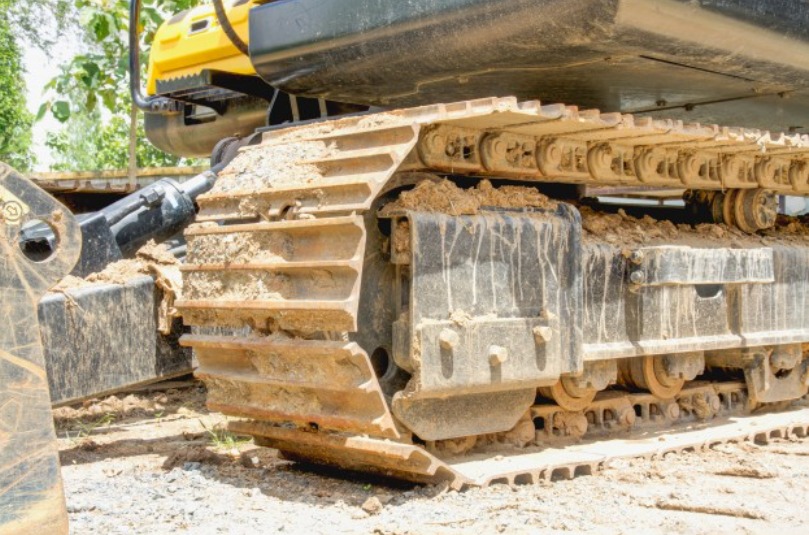
Perhaps the most obvious wear item on the excavator undercarriage is the track. The majority of compact excavators use rubber tracks and the life expectancy of the track is largely dependent upon the environment they are subjected to and the user’s operating habits. Tracks should be examined on a daily basis to look for cuts, tears or areas that expose the steel imbeds. Any perforations could allow moisture or contamination to enter the track.
The most important undercarriage interval item to monitor is track tensioning. A loose track is likely to de-track and will be detrimental to its useful life. Your operation and maintenance manual will indicate ideal track tension ranges and the correct way to position the excavator for making adjustments.
While other undercarriage components may not need daily inspections, regular monitoring of the components like idlers, rollers and sprockets can help identify potential problems in the early stage. Accelerated wear on the sprocket is not common; however, it should still be checked periodically by examining the teeth. A good sprocket tooth has a rounded end, while a worn tooth is more pointed. This is especially important to check when installing a new set of tracks.
5. Cooling system
An effective cooling system relies on adequate airflow and appropriate coolant level. If either is lacking, it can lose performance, cause an overheat condition — or worse yet — accelerate engine damage. Proper cooling system maintenance includes checking the airflow through the system and checking coolant hoses for leaks. The radiator, oil cooler and condenser can be cleaned by applying low pressure air or water, but use with care not to damage the radiator’s fins.
6. Electrical system
The electrical system of most compact excavators uses a 12-volt battery and fuses for the purpose of protecting this system in the event of an electrical overload. Always replace failed fuses with like kind and amperage rating. Battery cables should be tight and clean. Inspect for corrosion on the cable ends and the battery terminals. Prevention can typically be remedied with an appropriate dielectric grease.
7. Attachments and quick-tach mounting mechanism
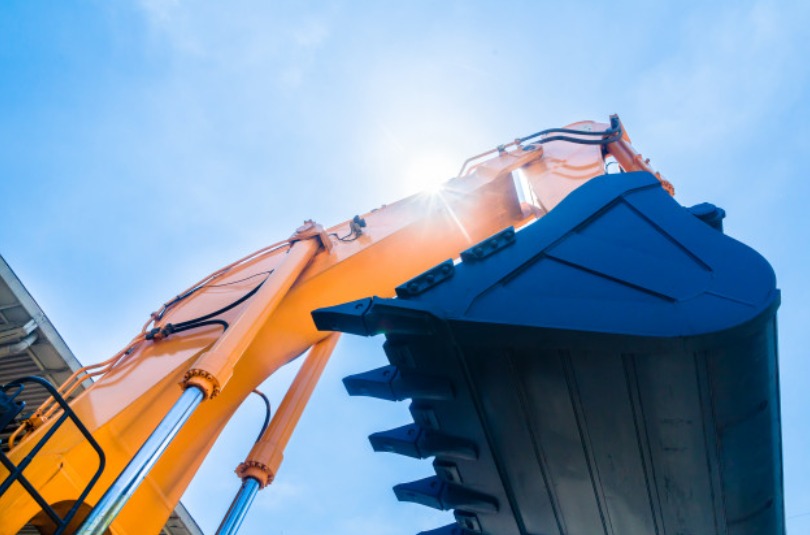
Visual checks of attachment components such as cutting edges, shanks, teeth and hoses on hydraulically powered attachments can help determine if where is developing or damage has occurred in tough, rigorous applications. Replace any worn or damaged pins or teeth to maintain productivity.
8. Instrumentation
Some compact excavators are equipped with on-board instrumentation systems with controllers that perform multiple maintenance-oriented functions. If the need arises, these systems can log and display machine vitals like fluid temperatures and coolant levels. These controllers can also warn operators when system parameters are out of sync, and they’re engineered to shut down the machine to prevent catastrophic damage if an operator does not heed warning messages.
9. Safety
Despite their compact size, excavators are rugged and versatile in a wide variety of conditions. Before starting the excavator for the first time, operators should understand what each and every lever and control does and how to operate the machine safely. Operators should always follow instructions for maintaining ROPS /TOPS cab structures and make sure their mounting hardware is secured. Other safety items like seat belts should be properly tensioned and in good working condition. Control console lockout systems should be functioning. Safety decals should be intact and legible, and all work lighting should be operational and visible.
Your compact excavator can be one of your most important investments. With their increased versatility and proper maintenance, they can generate revenue more hours of the day and more days of the year. By making a strong commitment to a manufacturer’s routine maintenance plan, you can add more useful life to your machine.
ARE YOU LOOKING FOR EXCAVATORS?
Please check our website:
http://yamada-co.jp/en/stock/
If you cannot find your desired unit, please send us inquiry from the below link:
http://yamada-co.jp/en/contact/
---------------------------------------------------------------
Japanese Used Trucks & Machinery Exporter
Yamada Sharyo Co., Ltd.
Website / Contact Us / About Us
Search Trucks / Search Machinery
---------------------------------------------------------------
- LATEST ARTICLES
-
-
2022.04.05
Mitsubishi Fuso Truck and Bus Corporation Introduces New "Euro 4" Compliant Lineup to Indonesian Market
-
2022.03.22
We Opened Facebook Page and Instagram!
-
2022.03.08
Recent Best Sell!
-
2022.02.22
Japanese made excavator brand ‘YANMAR’
-
2022.01.05
Special Announcement ~AUCTION & EXPORT SERVICE STARTS!~
-
- CATEGORY
- ARCHIVES
-
- 2022-04(1)
- 2022-02(1)
- 2022-03(2)
- 2022-01(1)
- 2021-01(2)
- 2021-06(2)
- 2021-03(1)
- 2021-09(1)
- 2021-07(2)
- 2021-08(1)
- 2021-12(4)
- 2021-11(1)
- 2021-02(2)
- 2021-05(3)
- 2021-10(2)
- 2021-04(3)
- 2020-04(8)
- 2020-02(4)
- 2020-01(4)
- 2020-07(4)
- 2020-05(3)
- 2020-12(2)
- 2020-08(3)
- 2020-10(3)
- 2020-06(6)
- 2020-09(3)
- 2020-03(5)
- 2020-11(2)
- 2019-01(3)
- 2019-12(4)
- 2019-08(3)
- 2019-11(5)
- 2019-04(7)
- 2019-02(4)
- 2019-05(4)
- 2019-06(4)
- 2019-07(3)
- 2019-09(4)
- 2019-10(4)
- 2019-03(3)
- 2018-02(4)
- 2018-05(4)
- 2018-06(7)
- 2018-10(4)
- 2018-07(4)
- 2018-11(5)
- 2018-09(4)
- 2018-08(4)
- 2018-03(5)
- 2018-12(3)
- 2018-04(6)
- 2018-01(4)
- 2017-12(8)